The Role of Materials Selection in Design
In materials science we hope to build upon students' understanding of physics and chemistry to show that materials are much more than their constituent elements. The structures that exist in materials, all the way from the nanoscale through the microscale, play important roles in the material behavior.
If you are working at the macroscale, like you will be if you are a mechanical engineer, aerospace engineer, bioengineer, environment engineer, or product designer, you may not need to think about these assemblies every day. However, the properties that arise due to these structural assemblies will very likely be something you need to consider most every day, if indirectly. Indeed, everything is made of something. In this sections, we'll explain where the question "what should we make this thing out of?" should arise in your work, and how to address it.
Most of you have had some sort of design experience at this point in your academic career. Perhaps you've designed an adaptive piece of equipment in DTC or fabricated rocket components for NUStars. Many of you may have competed in design competitions in high school. However, my suspicion is that very few of you thought about the specific materials that you'd make your product from with any real depth beyond "metal" or "plastic". But... there are well over 50,000 engineering materials to choose from! (Ashby, Introduction to Engineering Materials, 2012). Why are we limiting ourselves to so few when it is evidently clear that the material itself is pretty important. (Otherwise we wouldn't make new engineering materials or even have a field of MSE.)
The reason that you haven't been asked to do materials selection is likely because you have either: 1. only explored the early stages of a design project or 2. performance optimization was not critical in your design. Let's unpack 1. this by reviewing Ashby's model for Design Flow (Figure 14.3.1).
Figure 14.3.1 Design Flow Chart, indicating the three stages in design process that connect the market need to the product specification. The design tools and materials considerations at each stage. After Michael F. Ashby. "Material Selection in Mechanical Design." (2011).
Ashby organizes the design process into a linear process in which you identify a 1. market need, 2. develop a concept (i.e. a mechanism) to address this need, 3. select a specific embodiment to carry out the concept and 4. decide on the specifics of the embodiment. This leads to product specification. We'll show an example in a minute.
Along the way, you have to do a lot of work. You might have do to come up with prototypes and do viability studies. You may do computer models before building more advanced version of your produce. You'll want to do cost modeling to make sure that making the product makes sense. Those are all important. At the same time, you'll want to consider which materials will work for your product. In the beginning (and this is why you may not have considered materials much, yet, in your design projects) you don't want to limit yourself too much by the material! You'll analyze the possible materials with low precision. However, as your design takes shape, you'll need to consider specific subsets of materials, and ultimately you have to decide to make your product out of something.
Let's consider a common market need: sometimes people's backs are itchy and they can't scratch them with their hands. So, our market need is: "We need a product to relief people's itchy backs when they can't reach to scratch them".
So, let's begin:
- Concept: This is the working mechanism. There are lots of ways to eliminate an itch! One can scratch it, or apply an anti-itch cream. One can also heat or cool the area. Or, cause physical pain elsewhere on the body to reduce the itch. There are man concepts that we could use to address the market need.
- Embodiment: Let's say we've decided to provide mechanical sensory input to alleviate the itch at the spot. There are also many ways to do this: a reciprocating scratcher, a rotary scratcher, some sort of rolling massager, one that applies poking or needling pressure. These are all embodiments - they all address the issue of the itch with mechanical stimulation. And, at this point we start to see the limitations that materials might have. If we have a long object that allows us to scratch the spot, we'll need to make the material out of something stiff (so it doesn't bend) and lightweight. We will certainly also want to consider aesthetic and cost. This starts to limit our materials selection - perhaps to wood, plastic, or light-weight aluminum alloys.
- Detail: Once you've decided on a specific embodiment, you now must come up with the details: mechanical details such as dimensions, but also materials details. At this point you'll want to fully evaluate the options you have at hand, the different types of plastics or woods or aluminum alloys, to see which will be optimal for this selection when balancing it's mechanical performance, cost, and appearance. Only then can you actually make a product!
Balancing Selection Challenges
Whenever you make a product from a material, you need to consider some very important interconnecting issues:
- What function do we need the object to perform?
- What shape will my object take?
- How will I make, or process, my object?
- Which material will I use?
These are all connected to each other. For example, we noted above why the back-scratcher (the function) limits the materials I can use. In turn, the material I select will limit the shape I can make, or the process I use to create that shape.
An example: let's say I decided to make my back-scratcher out of ash wood. This is stiff enough to achieve the function. But, the mechanical engineers decided they want to make an extremely complex shape only achievable with additive manufacturing (process). Now this isn't possible with wood! I need to adapt my selection procedure (or the mechanical engineers need to adapt their shape or processing requirements) in order to decided on a usable material.
So, when we select a material we have to consider all of these function-material-shape-process interconnections to make a well-informed and optimal selection, as shown in Figure 14.3.2.
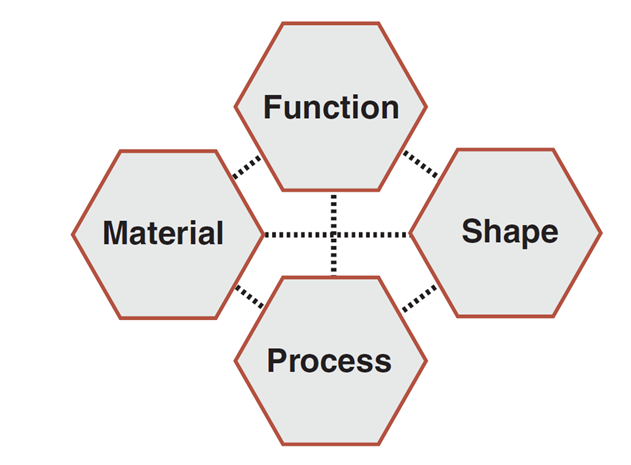
Figure 14.3.2 The interconnections between function, material, shape, and process are central to the field of materials selection.